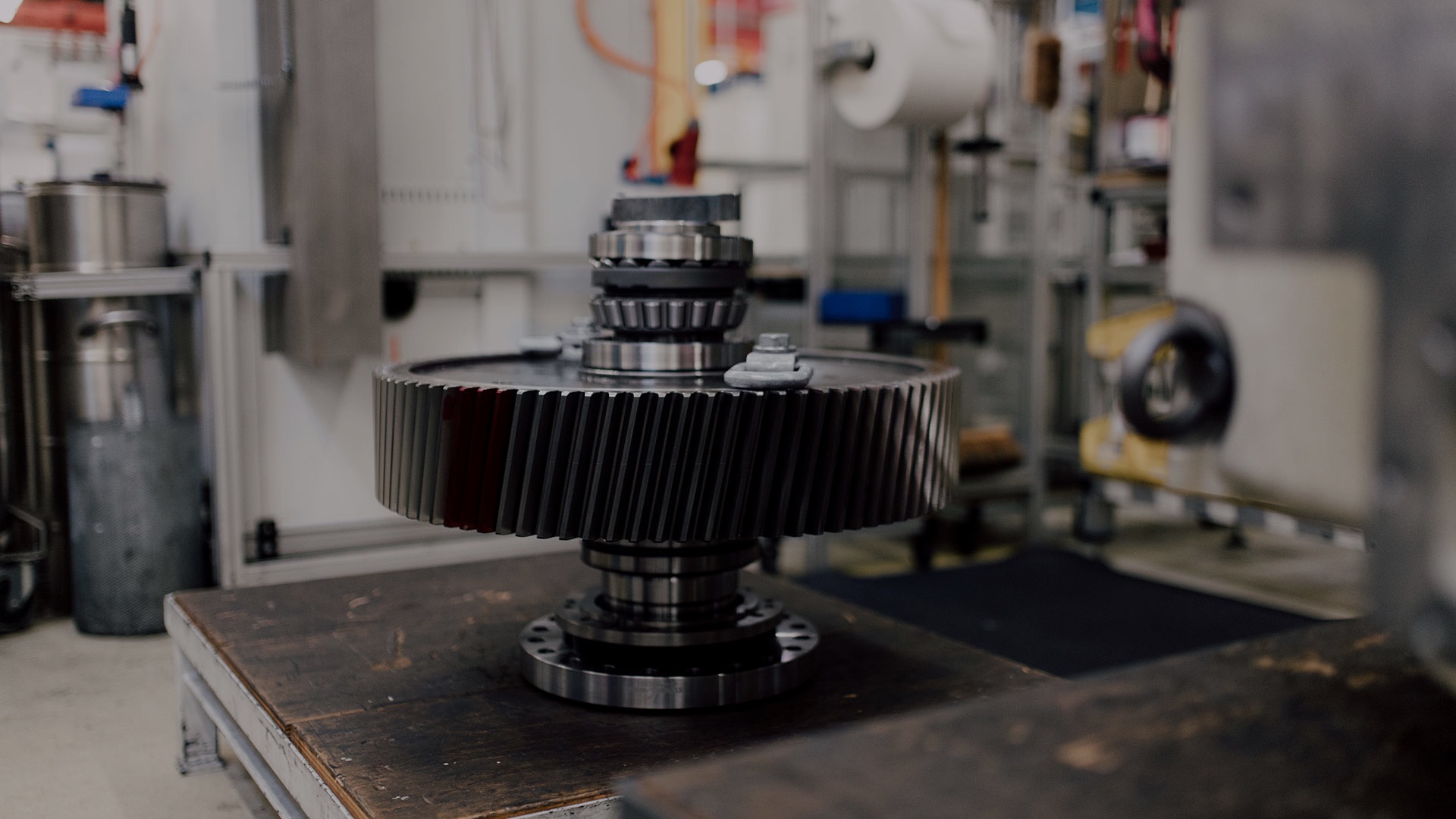
Get in touch with us:
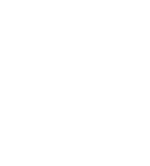
+49 5151 1040
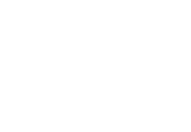
info@reintjes-gears.de
Service Hotline
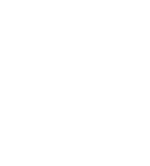
+49 5151 104104
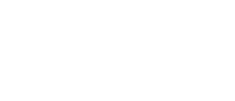
REINTJES GmbH
Eugen-Reintjes-Straße 7
31785 Hameln
Our next trade fair dates
09/01/2025 to 09/03/2025
Donsö Shipping Meet
Göteborg, Schweden
09/03/2025 to 09/05/2025
Expo Pesca
Lima, Peru
09/10/2025 to 09/12/2025
INMEX SMM India
Mumbai, Indien
09/17/2025 to 09/19/2025
Surabaya International Marine Offshore Expo SIMOX
Indonesien
”With a 3D printer, we save material and do something for the climate!”
Rising energy costs, high material requirements and international supply chains that are prone to disruption: Building marine gearboxes costs a lot of time and money. Are there perhaps manufacturing alternatives that save resources and money?
REINTJES GmbH is also faced with this question. And the experts for maritime gearboxes from Hamelin have developed a long-term solution. Klaus Deleroi, Managing Director of REINTJES, explains what this is all about.
Mr Deleroi, your industry - like the entire economy - faces huge challenges in the coming years. And it is precisely at this stage that you are presenting a solution with future potential.
That’s right. Together with a number of partners, we developed a large-format 3D printer as part of a research project funded by the German Federal Ministry for Economic Affairs and Climate Protection. The project took more than four years, and our share of the costs alone totalled around 450,000 euros. We now actually have a huge – and above all functioning – 3D printer in one of our production halls. The construction space measures four and a half by three by one and a half metres. That’s huge and really impressive!
You say the printer is working. So is it already running permanently and producing parts for REINTJES?
No. We are not allowed to integrate the device into our production processes because it is a research object and can therefore only be used for research purposes. And there is still a need for further development before the parts produced in this way would even be ready for the market. That is why we are currently working on a follow-up project.
That sounds more like a long-term solution. What time period are we talking about?
I can’t say for sure, I can only estimate. Perhaps in ten years‘ time we will be able to supplement and optimise our production processes with a 3D printer like this.
In which areas could you use a 3D printer?
3D printing has great potential, especially for customised products. We’re talking about customised housings for marine gearboxes. Thanks to 3D printing, we could counteract the large amount of material required, thus saving costs and also drastically reducing energy requirements. At the same time, we are no longer dependent on material deliveries, which can sometimes take many months. As things stand at present, however, such a device is of no use to us in series production.
Do you also have some figures for us in terms of actual savings?
At the beginning of 2023, we produced a gearbox housing part using the 3D printer as an example. Compared to the conventional production process, we were able to reduce the weight by around 36 per cent. The energy saving was also 41 per cent.
Why did REINTJES put so much effort into the development of a 3D printer in the first place?
There are two reasons for this: one emotional and one very pragmatic. The emotional one was that in 2015, when I had just started at REINTJES, I presented a small 3D printer at an event and talked about it. One of the guests at the event was Olaf Lies, who is now Lower Saxony’s Minister of Economic Affairs. And he told me that I had to think bigger. That spurred me on and I took it to heart. The pragmatic part of the story is: with such a large 3D printer, we save material – and therefore money – and make ourselves less dependent on suppliers. And we use less energy. That’s sustainable and we’re also doing something for the climate.
Info box: About the person
Klaus Deleroi (born 1969) studied marine engineering at Delft University of Technology (Netherlands) and has been Managing Director of REINTJES GmbH, based in Hamelin, Lower Saxony, since 2015. He previously held various positions at MTU Friedrichshafen (from 1996) and MAN Diesel (since mid-2008), among others.